Improve Coupling Capabilities
The CATHARE code is widely used in coupling with other simulation software by means of the ICoCo standard (itself compatible with the FMI standard). It can be coupled to CFD thermal-hydraulic codes such as NEPTUNE-CFD and its two-phase flow solver or TrioCFD to simulate more finely a part of a circuit. It is also used in multiphysics coupling processes such as the mechanistic code ICARE2 used for core degradation simulation, the thermo-chemical and mechanical code DRACCAR used for fuel rods simulation, the neutronic code CRONOS2 used for reactor core calculations or with the thermal code SAMCEF-Thermal used by our space partners.
Improve 3-D Module Capabilities
The 3-D module has been first developed to model the reactor pressure vessel for any accidental transient. Besides, one of
the main goal of CATHARE 3 is to improve it using
thin and non-conformal structured meshes. In CATHARE 3, it is possible to couple several 3-D modules (one for each component: core, downcomer, plena...) with different kinds of mesh. By example, a typical set of grids is: cylindrical 3-D grids for all the vessel components except the core, which will use a cartesian 3-D grids.
New optimized resolution methods have been developed in CATHARE-3 to couple 3D modules, and the input data-deck syntax has also been adapted to these new functionalities. Creating such type of modeling can be complicated for users, that is why the CATHARE team has improved the user graphical interface GUITHARE and the layout data of the 3D modules.
Specific applications require meshing with several thousands of cells, and the historical
CATHARE linear solvers developed for 1-D or 3-D modeling using a
coarse mesh become inefficient in these cases. To find a more efficient
resolution method, requiring less memory space, being less time consuming, and
getting more flexibility in the resolution method, CATHARE 3
has been interfaced to the PETSC library, providing interfaces to linear solvers such as MUMPS. Thanks to these numerical methods, it is now
possible to perform simulations with a large number of 3D cells, up to 20,000. A new architecture based on the CEA's open-source software development platform TRUST is also under study for 3-D simulations with CATHARE 3.
Improve 3-Field Model
A 3-field model is being developed in CATHARE-3, based on an extension of the two-fluid model. Three sets of mass, momentum and energy conservation equations are solved for the three fields: the gas or vapor, the continuous liquid, and the dispersed liquid flowing in the form of entrained droplets. This model has been first developed and assessed for vertical two-phase flows especially for dryout prediction. Specific correlations for the entrainment, deposition and for the estimation of the droplet size have been developed or introduced during the 2000' and validated against several experiments in tubes and rod-bundles. More recently, models of entrainment and deposition have been developed in the code, and models of the initial entrained fraction, i.e. the entrainment at the onset of annular two-phase flow, which has a significant impact on the prediction of the dryout, have been assessed against experiments.
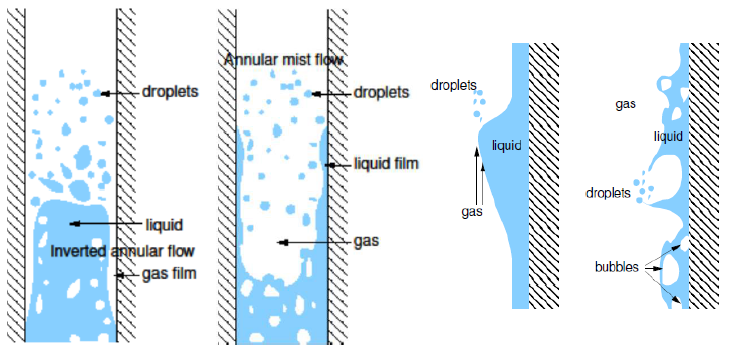